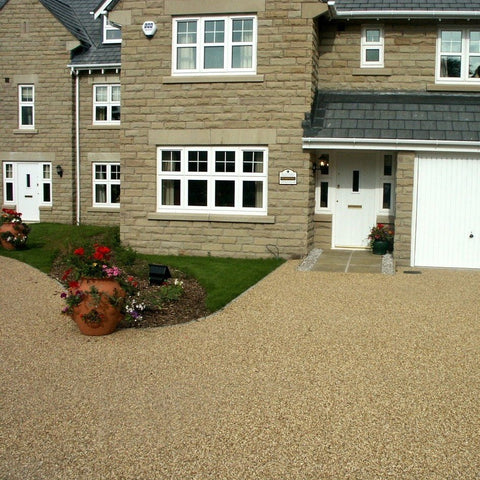
Flowbind UVR
Vendor: Virtus Resins
Flowbind is a high performance SUDS compliant porous aggregate bound system, incorporating a non-hazardous, fast curing, flexible solvent free resin and a range of aggregate blends. Systems cures to give attractive durable finish.
Uses
- SUDS areas
- Driveways
- Paths
- Swimming pool surrounds
Advantages
- High Strength System
- Porous/SUDS Compliant
- Range of Approved Aggregate Blends
- Excellent Track Record
- UV and non UV Stabilised Versions Available
Suitable Substrates
Firm, sound sub-base e.g. asphalt, concrete.
Available Options
Flowbind is available in 2 grades. Flowbind Standard is not UV stabilized and therefore will darken in UV exposure. The strength of the system is not compromised. Flowbind UVR is also available. This is an aliphatic system and is therefore colour stable when exposed to UV.
Components in the System
- 100kg decorative stone: (3 x 25kg bags of 2-4/2-5 mm stone + 1 x 25kg bag of 1-3mm stone)
- 6.5kg of Flowbind (UVR) resin OR 6.58kg of Flowbind resin
Coverage
4m² @ 15mm thick
Temperature Resistance
Resistant to temperatures of up to 50ºC for long periods.
Chemical Resistance
To various acids, diesel and petrol as well as strong bases.
Elongation @ Break (non-UV)
100% to BS2782 Part 3
Tensile Strength
Min 10 N/mm² to BS2782 Part 3
Speed of Cure 19ºC
Overnight
Aftercare
The surface should be swept regularly to keep it free of organic material such as leaves.
Mixing:
Mixing Instructions Resin: Prior to mixing, the temperature of the three components must be between 15 and 25 ºC. Pre-mix the coloured resin component before use. Add the hardener component to the coloured resin component and mix using a low speed electric mixer (200 - 500 rpm) for 1 - 2 minutes until homogeneous. Decant the mixture into a suitable mixing vessel and gradually add the aggregate component whilst continuing the mixing action. When all the aggregate has been added, mix for a minimum of 3 minutes until a uniform coloured, lump-free mix is obtained. Care should be taken to ensure that any material adhering to the sides, bottom and corners of the mixer is thoroughly blended in. Unduly extended or vigorous mixing should be avoided in order to minimise air entrainment.
Application:
The mixed PU resin should then be introduced into the mixer containing the aggregate. The aggregate must be dry (<0.5% moisture) and free from dust. While the mixer is running with the dry aggregate, add the PU resin at a ratio of minimum 6.5% up to 15% depending on end user requirements and the size and particle distribution of the aggregate – smaller particles, or greater particle distribution will require relatively more PU resin as the overall surface area is increased. Resin additions at these levels will ensure a well bonded, durable and sound system. A rotary mixer or low speed paddle mixer are suitable for mixing. Mix for 5 minutes until all of the aggregate is uniformly coated.
Application Instructions:
The blend of PU and aggregate should then be immediately applied to the surface and compacted with a trowel. The surface temperature should be between +10°C and +35°C for application (note comments above regarding the accelerator use for lower temperatures). The system should be applied at least 3°C above the dew point measured for the application surface. Care should be taken to ensure that the correct, even coverage rate is applied across the application area. This is especially important at high temperatures where the PU can be thinner. The surface should be installed at a minimum thickness of 3x the maximum stone grading used. Once levelled and compacted the surface can be smoothed with a trowel coated in a release agent, this allows for the top facing stones to be knitted together, giving an even surface
BLACK Basalt | HM QUARTZ | GREEN GRANITE | RED GRANITE |
SALMON PINK | BRITTANY BRONZE | AUTUMN GOLD | AMBER GOLD |
ALASKAN GREY | CORN FLINT | DOBBSWEIR | DOREST GOLD |
GOLDEN QUARTZ | GOLDEN TWEED | MULTI FLINT | DANISH QUARTZ |
BEIGE MARBLE | IVORY | CCKC | RHINE GOLD |